







Climate, environment and sustainability
Circular economy
The products of the German automotive industry are considered a benchmark in the circular economy.
The products of the German automotive industry are considered a benchmark in the circular economy.
We all want to be climate neutral as quickly as possible. The goal of the German automotive industry is to achieve a completely climate-neutral mobility by 2050 at the latest - in line with the Paris Climate Protection Agreement. The core technology of this transformation is electromobility, which the industry is working hard to ramp up to the market. But it is also clear: Without a circular economy, we will not achieve the goal of climate neutrality.
Despite the establishment of alternative drive technologies, CO2 hotspots remain in the life cycle of vehicles. Although hardly any CO2 is produced during operation, it is still produced during the extraction of the necessary raw materials, their further processing, logistics and in component and vehicle production. The vehicle value chain is very complex, with production and material supply chains for around 7,000 components and parts.
Therefore, strategies to reduce CO2 must extend beyond the vehicle's use phase. This holistic view of all stages of the value chain and their environmental impact is reflected in the "Design for Sustainability" strategies of the automotive industry. They include concepts for the extraction of raw materials, production, repairs, remanufacturing and recycling and are continued in the debate on the further development of the circular economy.

Five pillars for more sustainability
The following five pillars are crucial for a sustainable automotive industry with an integrated circular economy:
Resource conservation:
Material efficiency plays a major role in vehicle construction. Material efficiency strategies include, among other things, resource-saving product design, optimized production processes, material-friendly storage and recycling of materials. But the selection of the source of supply for the resources is also crucial. It is important to pay attention to the methods used to obtain, process and transport the raw materials.
Durability:
Vehicles are designed to operate for over 200,000 km. Some of them have been around for over 20 years, making them one of the longest-lasting consumer products. With new simulation methods in component development and innovative production processes, components can be designed to be even more resilient and long-lasting.
Repairability:
During vehicle development, care must be taken to ensure that the cars can be repaired with as little effort and cost as possible. The incurred repair costs often determine whether a vehicle should continue to be operated or replaced. This also includes a reliable supply of remanufactured spare parts for up to 15 years after the end of production of a vehicle.
Recyclability:
At the end of its life, at least 85% of the vehicle (as of today) is recyclable. This is a top value compared to other consumer products. This rate needs to be further increased by taking recycling into account when developing new vehicle components. What is the easiest and most efficient way to separate the raw materials used during recycling? And which new disassembly methods can be used and which processes can be automated?
Processing and reuse:
According to the data used by metal associations, around a third of a vehicle is already made of secondary material. This share can also be increased in the future. Especially with regard to the ramp-up of electromobility, it is also crucial to reuse batteries and, where possible, to recover lithium, nickel and cobalt for new batteries.

Stakeholders involved in the circular economy
In order to maintain a functioning circular economy, various players must work together closely and be able to exchange data with each other. This begins with information about the raw materials required and their extraction, both for the manufacturers themselves and for suppliers and development service providers. The latter also need to know how to design and produce the components desired by the manufacturers in a material-efficient manner.
But customers also need to be involved. There is already transparent information regarding product sustainability. In the aftersales area, workshop partners must have all relevant information and components available for repairs and services. And at the end of the vehicle life cycle, recycling partners are needed who dismantle the vehicles as efficiently as possible and feed as many raw materials and components back into the product cycle in accordance with current quality standards.

Material requirements in the automotive industry are constantly increasing
The products of automobile manufacturers and suppliers are already considered a benchmark for other industries. Manufacturers use high proportions of recycled steel and non-ferrous metals in new vehicles, have established high-volume remanufacturing processes, ensure very good repairability, promote the longevity of their products and ensure a significant reduction in hazardous substances.
But it is also clear: without a gradual increase in the resources recovered from the circular economy, especially in the area of batteries, this will not work in the long term.

According to current calculations by the VDA, with the current battery mix in 2030, vehicle manufacturers based in Europe alone would need around 50% of the global lithium production volume in 2030 in order to achieve a quota of 65% of electric cars in new European registrations. For comparison, in 2023 the share of cars produced in Europe corresponded to around 17% of the global market.
The situation is similar when it comes to semiconductors. In order to achieve the global market share of 20% in the EU for semiconductor production as envisaged in the European Chips Act, further significant public funding would be required by 2030. The automotive industry is currently only expecting around €30bn from the European Chips Act, which would lead to a global market share of less than 10%. The needs mentioned cannot be covered exclusively by future income from the circular economy. However, they can make a decisive contribution to making the automotive industry more resilient and thus accelerating the ramp-up of alternative drive technologies.
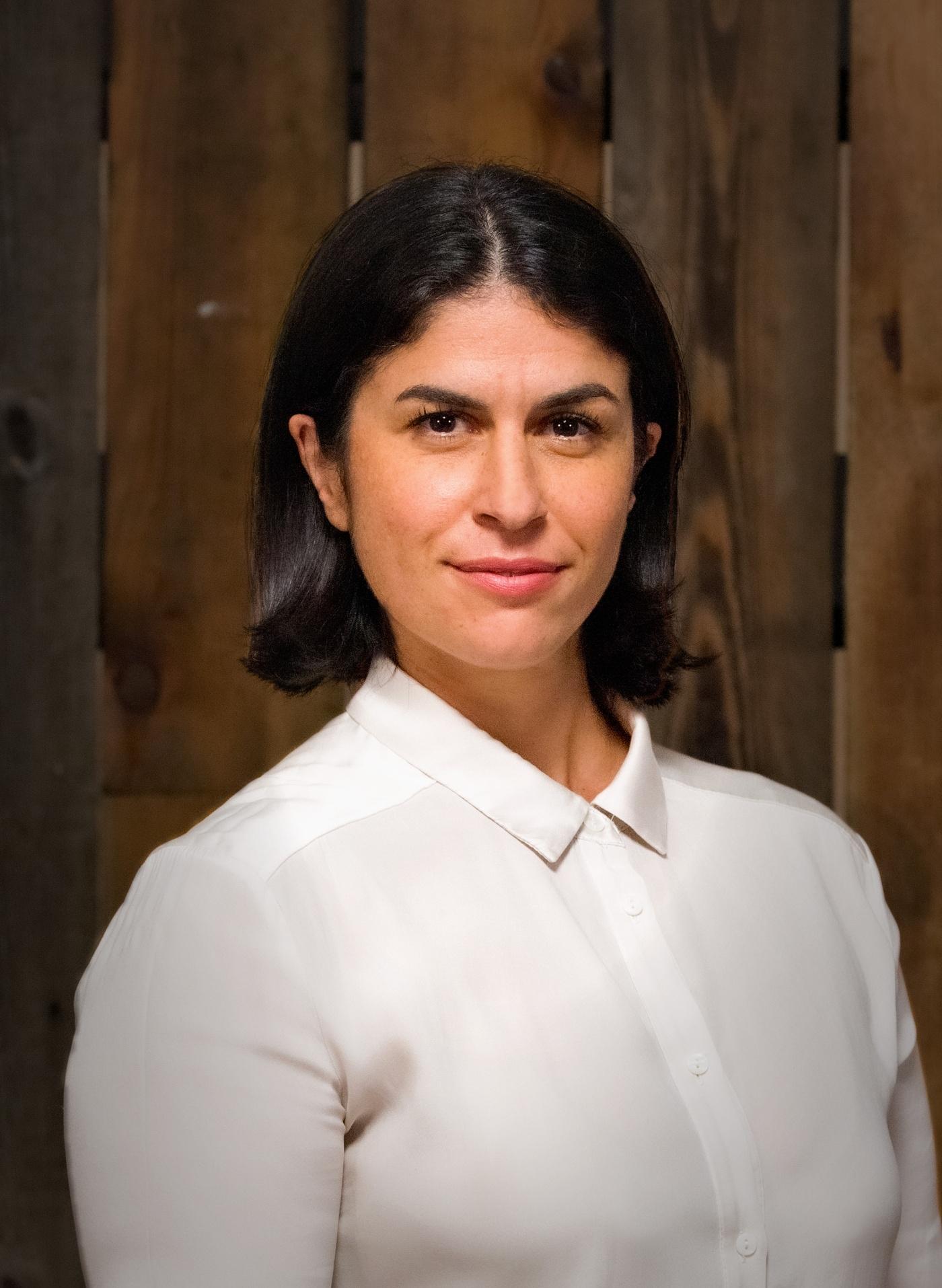
Dr. Evin Zozan
Specialist Circular Economy and Sustainability
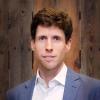
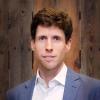
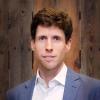
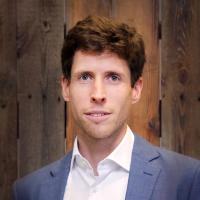
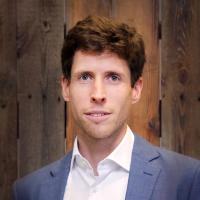