VDA Logistics Award 2023
VDA Logistics Award 2023: Prestigious award goes to Volkswagen AG for the 'MEB battery logistics' concept
Pressemitteilung
Pressemitteilung
Submissions from Bosch and Schaeffler highlighted by jury - VDA President Hildegard Müller praises "impressive innovative power of the automotive industry"
As part of the Automobile Logistics Forum (Forum Automobillogistik, FAL) in Herzogenaurach, the German Association of the Automotive Industry (VDA) presented the coveted VDA Logistics Award to Volkswagen AG. The company convinced the jury with the 'MEB battery logistics' concept and was voted this year's winner.
Every year, the VDA Logistics Award honors outstanding logistics solutions that serve as a role model for other companies in the automotive industry.
VDA President Hildegard Müller: "The VDA Logistics Award is the 'Oscar' of the automotive logistics industry - and every year it shows the impressive innovative strength of the automotive industry. The numerous applications are a clear sign of the creativity and entrepreneurial spirit of our industry. They also clearly demonstrate the attractiveness of this award. Congratulations to the winners!"
Müller further explained: "In times of increasing geopolitical uncertainties, mutually reinforcing crises and volatile developments, the automotive industry has to find even more innovative ways and solutions to master the diverse challenges and to turn the complex transformation on the way to climate neutrality into a success story. In these difficult times, logistics in particular is proving again and again how resourceful, flexible and decisive it is in tackling this change. This award and the impressive submissions demonstrate that our industry is successfully driving these advancements.
Due to its diverse composition of automobile production, logistics and supply chain management, the Forum Automobillogistik is the ideal event to jointly develop solutions and set the course for a successful future."
Winning concept: Volkswagen AG – battery logistics for modular electric drive kit (Modularer E-Antriebsbaukasten, MEB)
With the award of the 'MEB battery logistics' concept, the jury honors the bringing together of multi-innovations into an intelligent process chain. The aim of the future battery logistics concept is the cost-efficient and sustainable production and logistics of cell modules and battery systems. The basis for this is a standardized process together with the transport and storage technology as well as a lean, sustainable, cost-efficient and automated material flow that can be used repeatedly in all plants of the group.
The battery logistics of the Volkswagen Group achieves this by having logistics experts, experts from other departments and authorities work together at an early stage and plan and coordinate uniform premises for framework conditions that have not yet been finally defined.
At the same time, this creates a strong network between the battery assembly plants, the vehicle plants and, in the future, also the cell plants of the group brands. This creates synergies and promotes the transfer of knowledge.
The pilot plants include the plant in Braunschweig, which develops and manufactures chassis components such as steering systems, battery systems and axles, the Volkswagen plant in Zwickau and the main plant of the Škoda brand in Mladá Boleslav. Together, the three plants create a cost-optimized, environmentally efficient and standardized logistics process as a blueprint for all brands in the Volkswagen Group. David Strnad, Head of Logistics at Škoda Auto, who played a key role in the internationalization and optimization of the concept: "The award is a tribute to the commitment and excellent cooperation of all the logistics experts involved in the Group. Our joint battery logistics concept is both sustainable and process- and cost-optimized thanks to the use of rail as the main mode of transport and the automated loading and unloading of the wagons."
Impressive submissions from Bosch and Schaeffler
In addition to the excellent winning concept from Volkswagen AG, the jury particularly appreciated the submissions from Bosch and Schaeffler for their innovation and feasibility.
Bosch: Next Generation Transport Management
The Next Generation Transport Management (NGTM) project is an integrated platform in which suppliers, plants and logistics service providers are integrated. The strong integration with materials management offers advantages for all actors along the supply chain: For suppliers, e.g. the effort for transport orders decreases and logistics service providers can better plan their capacities through long-term forecasts.
The greatest advantages for Bosch result from procurement that is optimized for transport costs and CO2, shipment tracking based on materials, and automated processes in goods receipt and shipping.
Schaeffler: Transportation Data Cube
The logistics team at Schaeffler has looked into which means of transport and which transport route is the cheapest, most reliable, fastest and as climate-neutral as possible.
The solution is the Transportation Data Cube (TDC): From billions of pieces of data, the digital logistics tool filters those that are required to determine the optimal transport route. The user is able to adapt the structures of the data model flexibly and intuitively without IT knowledge.
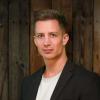
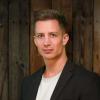
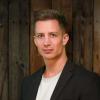
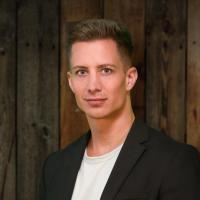
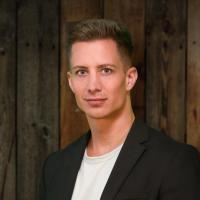