
Climate, environment and sustainability
Things to know about per- and polyfluorinated alkyl substances (PFAS)
The PFAS chemicals contribute to the achievement of the European climate goals in transport and strengthens Europe as a business location for the automotive industry.
The PFAS chemicals contribute to the achievement of the European climate goals in transport and strengthens Europe as a business location for the automotive industry.
PFAS are essential for production processes and products in the automotive industry
According to the definition of the European Chemicals Agency, the chemical group of per- and polyfluorinated alkyl substances (PFAS) includes at least 10,000 chemical substances that are characterized by a number of specific and useful properties. Above all, this includes a particularly strong resistance to heat, cold, grease, dirt, friction, oil and water as well as a very high stability, which is why they are also referred to as "eternal chemicals".
Through the responsible use of PFAS in the automotive industry, emissions into the environment can be largely ruled out during the entire life cycle of the vehicle. If emissions occur, accidents are the cause. The use of PFAS is indispensable for today's vehicle concepts as well as for the ramp-up of electromobility.
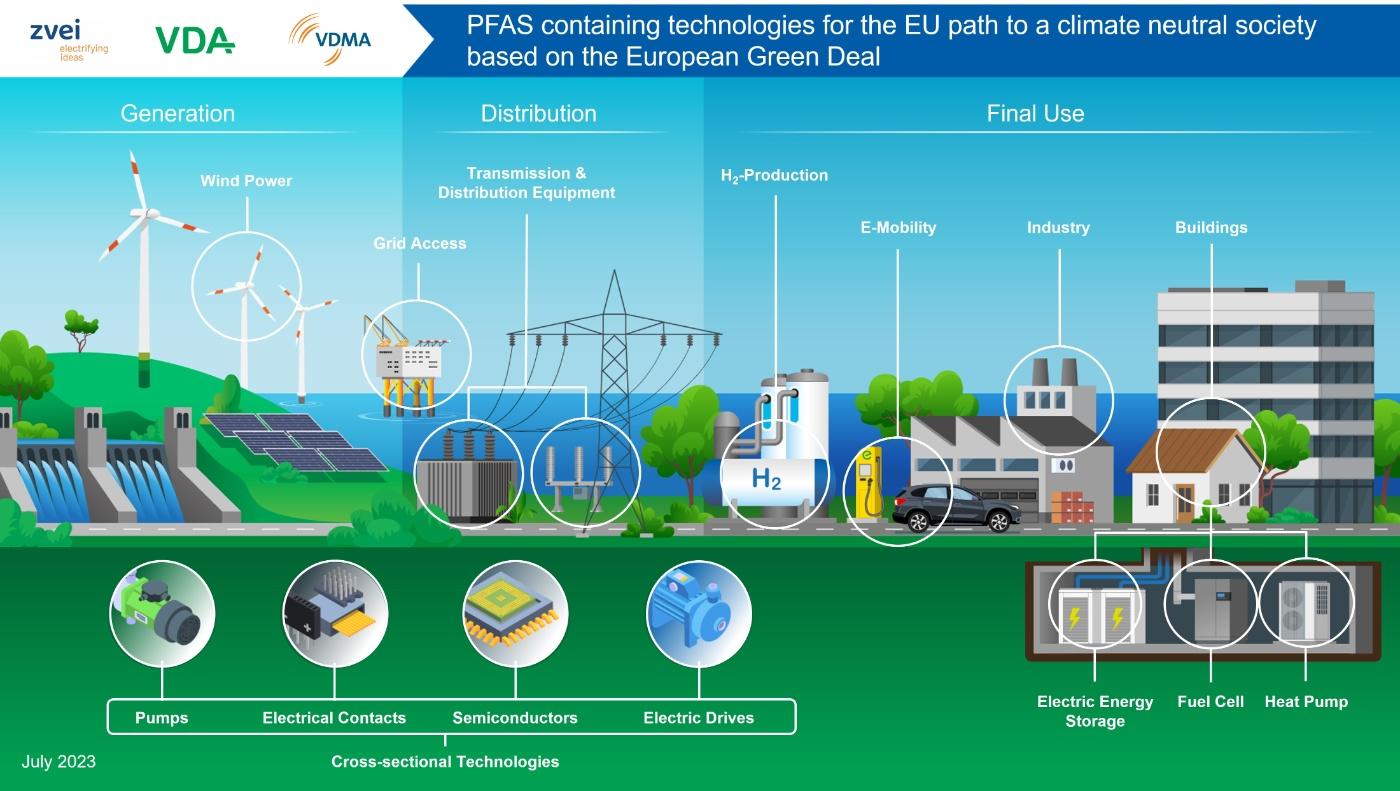
Due to their unique properties, PFAS are used in a variety of ways in the manufacturing processes of the automotive industry as auxiliaries and components of intermediate and end products. The substance group of PFAS ranges from polymers to gases (non-polymers) with very different environmental and health risk classifications. Unlike as is often assumed, there is no homogeneous substance group of PFAS.
Polymers
Within the PFAS group of substances is the group of fluoropolymers. Also known as fluoroplastics, these chemical compounds consist of a main carbon chain to which several fluorine atoms are directly bonded. They are characterized in particular by their high resistance to other chemicals and moisture. The former is essential, for example, in the manufacture of computer chips to prevent contamination of the metal ions, while the latter property is primarily needed in the semiconductor industry to make electronics watertight. These applications are also indispensable for modern drive systems. Due to their unique property profile, fluoropolymers are used in a variety of ways in the automotive industry: from Li-ion batteries to power electronics, elastomers, lubricants and processing aids.
The OECD classifies 38 fluoropolymers, including PTFE and PVDF, which are frequently used in the automotive industry, as “polymers of low concern” (PLC). Fluoropolymers classified as PLC pose no risk to the environment or human health.
Non-Polymers
A distinctive chemical structure of PFAS arises when a functional group such as carboxylate or sulfonate is attached to the end of a fully fluorine-occupied carbon chain. In this case, so-called non-polymeric fluorocarbon compounds are formed, which differ from polymers in their properties and risks. These include, above all, the perfluoroalkyl acids (PFAA), which are of crucial importance for the production of textiles, membranes and fluoropolymers. In the past, perfluorooctanoic acid (PFOA) and perfluorooctane sulfonic acid (PFOS) were widely used, but these compounds have been subject to strict restrictions in the EU since 2006. Accordingly, they hardly play a role in the automotive industry anymore.
Non-polymer PFAS are hardly ever used in modern vehicle technologies. The exception here is the refrigerant tetrafluoropropene (R1234yf), which is used in air conditioning systems.
Vehicles and their components go through these three phases: manufacturing, utilization and recycling. In each of these sections, PFAS play a crucial role.
Manufacturing phase
PFAS are used in production in numerous electromobility components. As components of products, they ensure their functionality and as production aids, they ensure suitable framework conditions for production processes.
Accumulators, which are required to drive electric vehicles, mostly occur in the form of lithium-ion batteries. PFAS are required here on the one hand as a binder for coating the cathodes with metal oxides and on the other hand as a protective layer between the anodes and electrolytes.
In fuel cells, in high-voltage and microelectronics and in technical textiles, manufacturers also use fluorocarbon compounds for bonding and coating and as heat, water and dirt-resistant membranes for various components.
In the case of semiconductors, the production process requires clean room conditions, which are made possible by the use of fluoropolymers in tanks, valves, pumps and pipes. In addition, the tools used require resilient resistance to moisture and various chemicals, which is guaranteed by PFAS.
In all cases, the production of the key technologies takes place in closed plants, so that emissions into the environment are not to be feared during normal operation.
Utilization phase
In traction batteries, high demands must be met during operation in terms of service life, charging speed, high energy density and persistent charging capacity, usually with large temperature and energy fluctuations. PFAS are essential for these requirements due to their stability, heat resistance and durability.
Fuel cells form a highly reactive environment with sometimes acidic conditions in the vicinity of the catalyst. In this environment, PFAS are required as a resistant, proton-conducting material, for which no alternatives with the necessary technological maturity are currently available.
Both the battery and fuel cells are encapsulated and sealed. The same applies to the majority of other places of use, which means that emissions of fluorocarbon compounds can be largely ruled out and limited to accidents.
The refrigerant tetrafluoropropene (R1234yf) currently used in vehicle air conditioning systems escapes into the environment in small quantities during regular operation. In addition, in the event of a fire, hydrogen fluoride can form and be released. The risk to humans and the environment from these emissions has not been conclusively clarified.
Recycling phase
When a vehicle has reached the end of its life cycle, it is disposed of in an environmentally friendly manner. After the vehicles have been accepted by a certified dismantling company, they are drained of fuel, engine oil and brake fluid which are all collected and professionally disposed of. Subsequently, usable spare parts, the traction battery and components containing pollutants such as the starter battery are removed. Then the remaining body is pressed and taken to the shredder. After the car bodies have been shredded (along with other consumer items such as refrigerators), the materials are sorted and fed into the material cycle. Non-recyclable materials, often plastics, rubber or glass, are thermally recycled.
This ensures that components containing PFAS are treated properly in the recycling phase also. They are either properly disposed of and processed, reused (e.g. as used spare parts) or completely decomposed due to the high temperatures in the thermal incineration plants. The resulting fluorine compounds are removed via gas scrubbers.
In addition, there is already a chemical process for fluoropolymers that can close the chemical product cycle through upcycling. They are broken down into gaseous monomers via pyrolysis. These can then be captured, purified and reused to produce new polymers without any loss of quality.
For most applications in the automotive industry, there are currently no technically mature alternatives for the specific application. This also applies to the use in traction batteries, fuel cells or power electronics.
In the case of fluoropolymers, for example, any replacement would inevitably cause a deterioration of the greenhouse gas balance, because other materials cannot guarantee the high resistance to abrasion and wear. This in turn increases frictions and maintenance requirements during operation. In the worst case, products would have to be replaced prematurely.
PFAS-free alternatives are conceivable for refrigerants and are already being used in a few vehicle models. However, with the substitution of the refrigerant, a completely new thermodynamic layout of the air conditioning systems, as well as new components, are necessary.
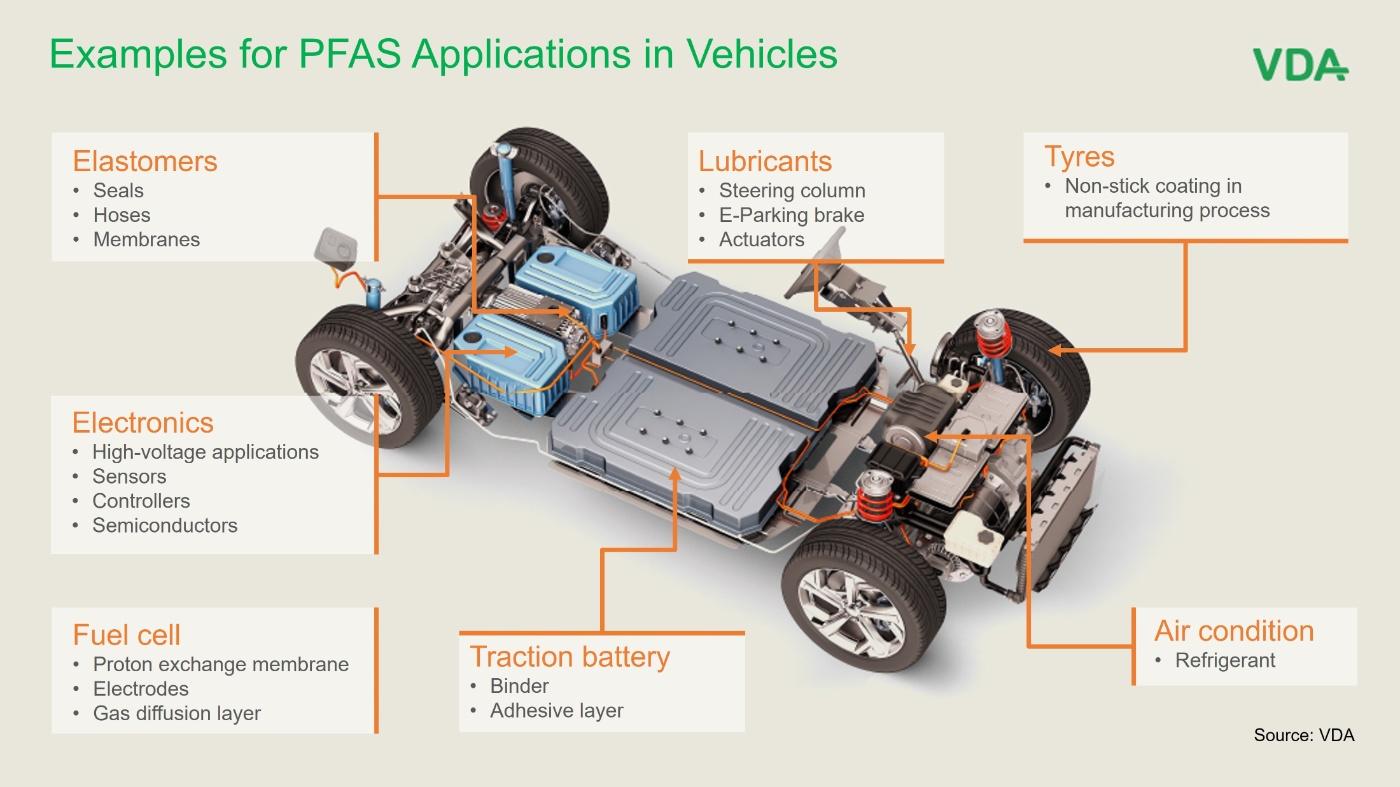
Concept of responsible use of PFAS
The automotive industry advocates responsible handling of PFAS in its operations. This concept includes:
- a phase-out roadmap for polymeric and non-polymeric PFAS with risks to humans and the environment, including substitution options,
- a review process for polymeric and non-polymeric PFAS with risks for humans and the environment where substitution options are currently unavailable,
- a general exception of fluoropolymers due to their low risk (OECD classification "polymers of low concern"),
- a general exception of spare parts based on the "repair as produced" principle,
- Enabling the re-marketing of used cars and parts in line with the European waste hierarchy,
- the openness to innovation, enabling the use of PFAS with low risk in new technologies and applications that are not yet known, and
- Encouraging investments in plants with best available technologies in recycling and waste treatment.
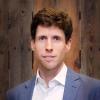
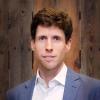
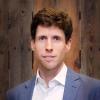
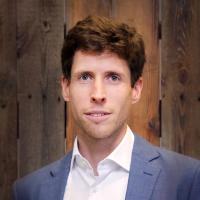
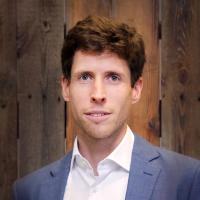