- Topics
- Automotive industry
- Market developments
- Automotive industry domestic manufacturing

Market developments
Transformation enables turnaround in domestic production
- Topics
- Automotive industry
- Market developments
- Automotive industry domestic manufacturing
Domestic production breaks negative trend
2022, domestic production expanded again for the first time since 2016. Various factors were responsible for this. Firstly, at 3.1 million, the level of domestic production in 2021 was the lowest since 1975. Incentives for electric cars, which expired or were reduced at the end of the year, particularly in Germany, led to purchases being brought forward, which boosted production,
particularly in the final quarter. Furthermore, a manufacturer of electric vehicles which started production at a newly established site additionally made a small contribution to the growth in domestic production. Last but not least, the order backlog was at record levels and supported production sustainably.
In 2022, production volumes were again hampered mainly by supply bottlenecks affecting all car manufacturers in Germany. The main factor here was the continuing semiconductor shortage, which is only easing slowly. The German location was particularly hard hit by this. This was due to the strong focus on premium products, which, like electric drive vehicles, require an above-average number of chips for assistance systems, screens, control units, etc. For the year as a whole, domestic production increased by 12 percent, but at 3.5 million passenger cars it did not even reach the level of the 2020 corona year, meaning that production has lost almost 1.2 million units since 2019 alone.
E-cars overtake diesel
For the first time, more electric passenger cars (including plug-in hybrids) than diesels (22 percent) were produced in Germany in 2022, accounting for 25 percent of domestic production. Even gasoline-powered cars, whose share fell from 55 percent to 52 percent, were not spared from the trend toward e-mobility. As you can see, the German location is at the forefront of the transformation, but traditional combustion engines remain an important mainstay for cushioning the abrupt shift toward CO2-free mobility, which in some cases has drastic consequences for the workforce, especially at suppliers.
In addition, for many years there has been a strong trend towards efficient compact SUVs. However, the production of new models in this area has recently been located by German OEMs mainly in other European countries.
The production of small and compact cars in Germany has been declining for many years. The very high labor costs, which stem to a large extent from the considerable additional wage costs, are primarily responsible for this. Brexit has also meant that a formerly important customer for smaller cars has lost significant importance.
In the global country ranking by unit sales, Germany holds sixth place behind China, the USA, Japan, India and South Korea. However, it should be noted that the premium share at German locations is very high. In Europe, Germany remains by far the most important production country.

Production of German OEMs abroad on course for consolidation
After two years of declining production figures, production by German passenger car manufacturers abroad increased again for the first time in 2022. At 9.6 million passenger cars, the previous year's result was exceeded by 2 percent. However, the production level is still below that of the first Corona year 2020, when 9.8 million passenger cars rolled off the international assembly lines. The dominant issue in 2022 remained the shortage of semiconductors, which meant that far fewer vehicles could be produced than the market would have allowed. Worldwide, almost one in five new cars bore the corporate logo of a German Group brand.
Heterogenous development in the countries
A look at the various continents reveals that the situation in the individual countries was quite heterogeneous, and the various regions were affected to varying degrees.
The largest location, China, made a decisive contribution to the increase, with foreign passenger car production by German OEMs rising by 5 percent to 4.47 million units in 2022. Here, the 18 percent drop in the first quarter due to corona lockdowns, particularly in Shanghai, was more than compensated for in the remainder of the year.
In Europe, 2022 foreign production continued to crumble by 2 percent to 2.93 million passenger cars, down nearly 1.05 million vehicles from the 2019 record. Demand would have allowed for significantly higher production, but unfortunately the limited supply of semiconductors did not allow for higher production volumes. In terms of countries, Spain again took the lead with 740,000 units (+9 percent), ahead of the Czech Republic with 693,000 units (+2 percent). Hungary followed in third place with 323,000 units (+4 percent), ahead of SUV hub Slovakia, which fell back somewhat with 269,000 vehicles.
Foreign production in America stagnated last year at 1.79 million vehicles (-1 percent). While U.S. production was down 6 percent to 824,000 units, production in Mexico expanded 9 percent to 634,000 units. In the USA, these are almost exclusively SUVs, and in Mexico to a predominant extent SUVs, which are sold worldwide in each case.
Transformation and premium strategy
The transformation from combustion engine to electric drive is also reflected in the foreign activities of German manufacturers. Last year, 896,000 e-cars (+18 percent) were manufactured outside Germany, slightly more than in Germany. The momentum came primarily from BEVs, which realized a growth of 37 percent to 513,000 units. PHEV production, on the other hand, stagnated at 383,000 units (-1 percent).
Production outside Germany has almost doubled since 2009, overtaking domestic production in 2010. The Corona crisis has meant that almost three quarters of all passenger cars produced by German OEMs are now made outside Germany. A key success factor has been the focus on premium models. Whereas in 2006 only one in five cars produced abroad was a premium model, it is now one in two. The global positioning of German OEMs is also reflected in the fact that they now manufacture 4.8 million premium cars abroad, twice as many as at their home base.

Germany has the world's highest labor costs in the automotive sector
The high quality and increasing complexity of modern passenger cars manufactured in Germany (due to sophisticated assistance systems and increasing digitalization) has its price. Furthermore the structural shift towards electromobility is in full swing. In order to remain attractive to the highly competitive skilled workforce, automotive companies in Germany must offer attractive remuneration. In 2022, Germany again had the highest labor costs in the automotive industry in an international comparison, at just under 59 euros per hour (+1 percent year-on-year). The Netherlands followed in second place at 56 euros (+6 percent), with labor costs having risen massively since 2016. High-wage Sweden ranked third with labor costs that crumbled by 2 percent to 50 euros in 2022. The weakness of the Swedish krona was the main contributory factor here.
With the labor costs going up by 25 percent in the past ten years Germany increases have been relatively high. Thus, there is a risk that Germany will lose the competitiveness regained through wage restraint in the course of Agenda 2010. Inflation, which has picked up particularly sharply in Germany recently, is exerting further pressure on wages and salaries and thus on labor costs. Domestic production, which increased by 12 percent in 2022 but lost more than 2 million cars compared with 2017, at 3.5 million, remains under strain.
Austria comes in at No. 4 in the ranking with 46 euros (+5 percent), ahead of France with just over 45 euros (+2 percent) and Belgium with 42 euros (+6 percent). Belgium is the only EU member state where labor costs have fallen since 2012 (-6 percent). In the UK, labor costs have increased by 7 percent to almost 39 euros in 2022. However, labor costs are still below the 2015 level. The Brexit referendum had led to a significant devaluation of the pound in 2016/2017, from which the British currency has not recovered substantially to date. In Italy, labor costs rose by 2 percent last year and, at 32 euros, are now back at the 2020 level. Spain also saw a rebound after the 2021 decline, with labor costs rising by 2 percent to 28 euros.
Eastern European countries converge slowly
At the bottom end of the labor cost table are Eastern European countries with labor costs between 10 euros (Romania) and 21 euros (Slovenia and Czech Republic). These emerging automotive nations have seen high increases of between 42 percent (Hungary) and 112 percent (Romania) since 2012, so labor cost levels are gradually converging with other EU countries. In Portugal, labor costs have risen by 5 percent to just under 17 euros in 2022 and lie between Hungary (13 euros) and Slovakia (18 euros).

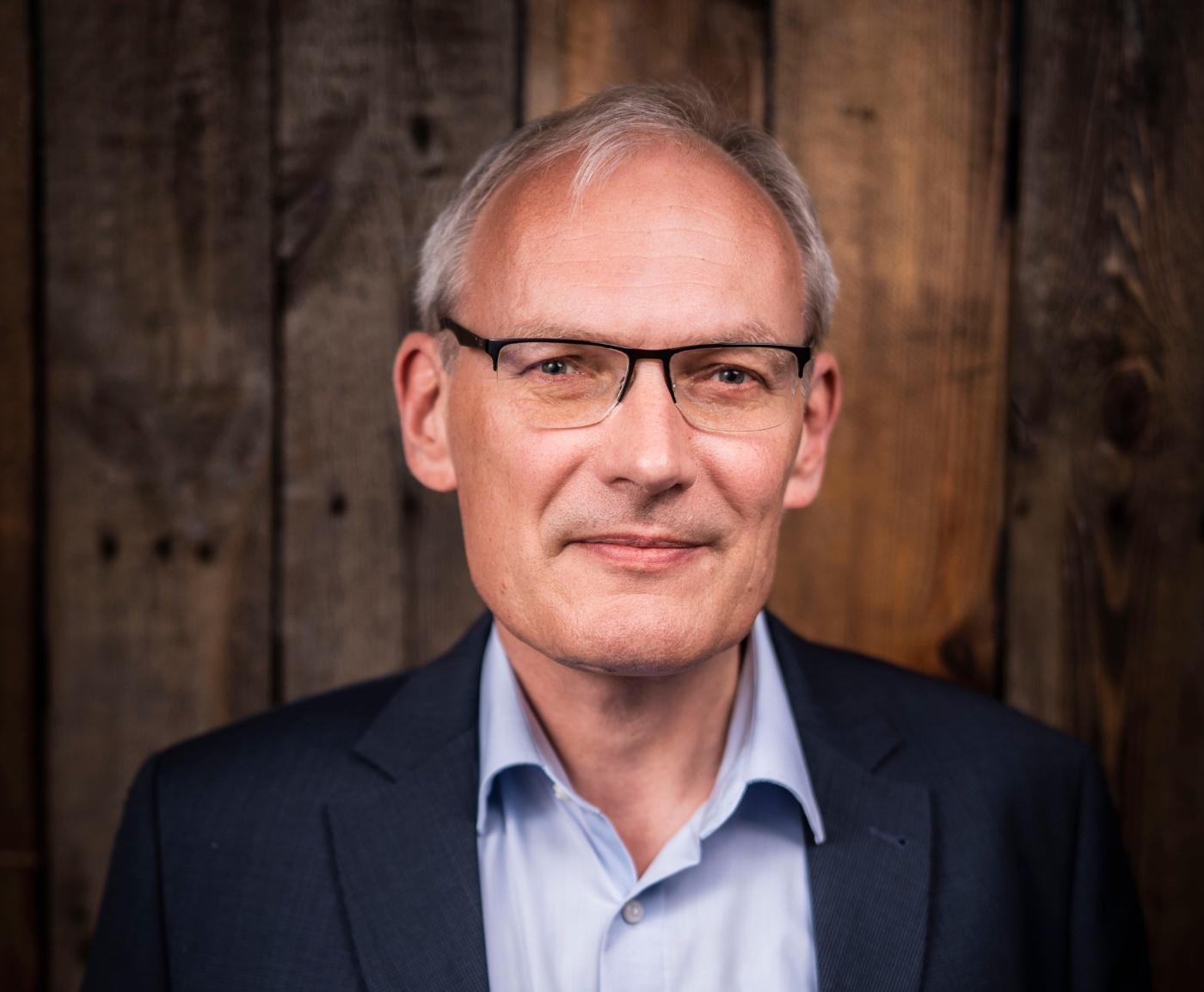